ENGINEERED TO SUCEED
Composite Cold Expansion Tool
In the world of aircraft manufacturing, cold expansion products literally hold these aircraft together. The problem faced today is that the Little Brute Hydraulic Puller designed and built by Fatigue Technology Inc. is a handheld steel hydraulic cylinder that is heavy and expensive to produce. In a market that demands continuous improvement, there is a constant push to make the product cheaper, better and lighter. In order to accomplish this demand a composite tube will be substituted in the design as the primary pressure cylinder instead of the traditional steel pressure cylinder in order to create a lighter and cheaper design.
Two separate designs we have been designed and built to withstand a given test pressure which will correlate to the sample provided by Polygon Composites.
The first design is a single acting single cylinder that has caps at both end which extend past the outside diameter of the cylinder and will use bolts to hold the caps together. The second design will be similar however, the caps will thread onto an aluminum sleeve fitted outside the composite cylinder. The purpose of the aluminum sleeve will be to determine if the sample can meet the strength requirements with or without the extra layer.
Each cylinder will be loaded until failure and the load will compared to a theoretical value established based on the dimensions of the sample. Both designs will be analyzed to determine their potential weight savings, cost of manufacturing and its potential improvement in machining and assembly time.
![]() | ![]() | ![]() |
---|---|---|
![]() | ![]() | ![]() |

Little Brute Redesign using Composite Materials by FTI
Project Goals
The premise of this experiment is determine if manufacturing a functional Little Brute will:
create a significant amount of weight savings (at least 25%),
Comparable in strength to the current model (6ksi no failure and at 10 ksi with no rupture).
decrease manufacturing costs, and
decrease manufacturing time.

Analysis
Construction
The first phase of the prototyping of the composite little brute will be largely focused on material testing and static load conditions.
​
The first designs are single acting hydraulic tubes where the composite material provided by Polygon Composites is the primary pressure vessel. Each specimen will be loaded until failure and the data generated will yield answers to several of our questions.
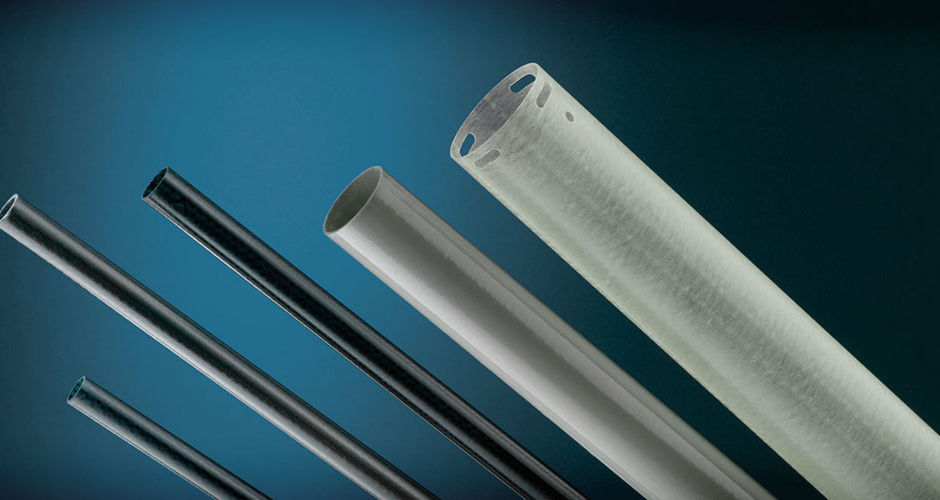
Results
Defining Success
The test was deemed a success based on the previous criteria. A failure was detected at 8000 psi when weeping at the bottom end of the tube was observed. The test itself took approximately 57 minutes to complete and was loaded to 10,000 psi at which point the hydraulic press was at its maximum operating pressure. The test was performed on site at Fatigue Technology inc. in Tukwila, WA.
The resources and procedures used in the actual test followed the test plan almost exactly.
From observation, the test was a success and so much so that the composite tube with an additional aluminum sleeve did not need to be tested. IT was assumed that if the unreinforced tube could sit at the maximum operating pressure with no structural failure that the stronger specimen would be as well.
In addition to our testing success, the data showed that when it was plotted on a stress-strain diagram to be linear. This is one of the most important outcomes of the test because it suggests that the material deformed elastically. Plastic deformation would have meant that the second phase of development for the double acting hydraulic cylinder would not be able to continue.
​
In accordance to our weight savings goal, the specimen weighed 72% less than the same design made out of steel. The Aluminum reinforced design yielded a 29% reduction in weight. Both crossed our threshold weight savings goal of 25%.
​
The goal with the composite design was that an "off-the-shelf" product could be selected and from there adapted into the little brute design. The sample provided by Polygon is extremely useful in the terms of functionality of the Little brute phase 1 prototype. It has an impeccable surface finish that is ready to use in hydraulic applications without additional machining of the inside diameter. However, during the process of parting the sample on a lathe, there were Three major problems. The first was that the fiberglass composite does not form chips like a metal would. Instead, the debris was more like dust and required a second operator to stand next to the lathe with a vaccum in order to keep the air free of said debris.
​
The second problem was the circumferential wrapped fibers started to come apart. This caused additional material to be lost to the machining process than just the material being removed from the parting tool.
The third problem in conjunction with the second was that the material was very difficult to rework. The loose fibers from the parting operation had to be removed and in order for an adequate surface finish to be restored it had to be worked down using several abrasive methods. After breaking a belt off of a small sander, a dremel was used to grind down the remaining fibers. The corresponding dust lodged itself in the pores of the dremel head rendering the abrasive head virtually unusable for other operations.

Budget and Schedule
Quarterly Goals and Overall Budget
1st Quarter Goal
Identify a suitable manufacturer of composite materials
Design the testing apparatus
2nd Quarter Goal
Obtain material and construct the test specimen
3rd Quarter Goal
Present findings
​
Budget
Planned: $1000.00
$800.00 for composite parts​
$200.00 Aluminum fittings
Actual Budget:
$0.00 for composite parts (donated)​
$0.00 aluminum fittings (machined out of scrap parts)
>$5.00 for screws and nuts.
Contributors
​
A special thanks to FTI for sponsoring and mentoring me during this project. Without the help of FTI's R&D engineer James Ross, this project would have not gotten off the ground.
​
Another round of thanks goes to FTI for their donation of materials, the use of their machine shop and testing facilities.
​
​
Thanks to their generous donation of Polyslide fiberglass composite tubing, this project was possible.